ISO standards are globally recognized frameworks developed to improve how organizations manage quality, risk, safety, and efficiency. Aligning with an ISO standard is a way to operationalize control, build trust with customers and regulators, and create systems that scale.
The International Organization for Standardization (ISO), an independent non-governmental entity, publishes these standards. The standards themselves are not enforced by ISO. Instead, third-party certification bodies assess and verify whether your organization’s systems meet the required criteria. When your company meets those criteria and passes the audit, you’re considered ISO 9001 certified, confirming compliance with all applicable ISO 9001 requirements.
Why organizations adopt ISO standards
When quality issues, inefficiencies, or market access barriers emerge, ISO standards provide a structured path forward. Adopting a standard like ISO 9001 is often driven by external demands — customer expectations, tender qualifications, or partner requirements — but the internal benefits are just as impactful. Stronger process control, clearer documentation, reduced rework, and improved customer satisfaction are all real outcomes.
What ISO certification actually proves
Being ISO 9001 certified shows that your company’s Quality Management System (QMS) has been built to meet the full set of ISO 9001 requirements, and that it’s implemented, monitored, and continually improved. It signals to clients and regulators that you’ve committed to a repeatable, reliable way of working — not just a one-time fix.
Key ISO standard types manufacturers care about
- ISO 9001 – Quality Management Systems
- ISO 14001 – Environmental Management
- ISO 45001 – Occupational Health & Safety
- ISO 27001 – Information Security
While dozens of ISO standards exist, most manufacturers begin with ISO 9001. It sets the foundation for operational discipline and is often a prerequisite for industry-specific compliance.
The process at a glance
The path to meeting the ISO 9001 standard involves five key phases:
- Preparation and planning
- Documenting your management system
- Implementing and operationalizing processes
- Running internal audits to assess compliance
- Undergoing a third-party audit and maintaining conformance over time
Each phase builds on the last — and each is grounded in specific clauses from the ISO 9001 requirements. The steps may seem linear, but in practice, the process is iterative, reflective, and deeply tied to how your team operates day to day.
Getting ISO 9001 certified isn’t a paper exercise. It’s a transformation of how your organization manages risk, quality, and improvement — one that pays off through better outcomes and stronger trust with every stakeholder.
How to Get ISO Certified - Step-by-Step
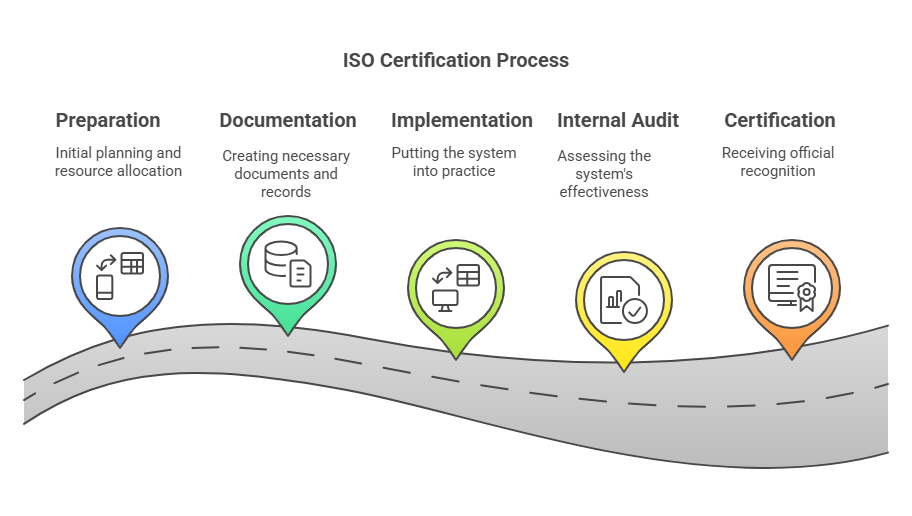
Step 1: Preparation (training, gap analysis, planning)
Before implementing any systems or procedures, teams need clarity on what's expected. The ISO 9001 standard outlines requirements related to leadership, planning, risk, performance evaluation, and improvement. But without proper orientation, these can feel abstract.
Start by building internal awareness. Train key stakeholders — quality managers, operations leads, and executive sponsors — on the core structure of the ISO 9001 requirements. Use resources from accredited bodies or specialist platforms to understand what compliance really involves.
From there, conduct a gap analysis. This means comparing your current procedures, documentation, and workflows against each clause of the ISO 9001 standard. The goal isn’t just to identify what’s missing — it’s to understand what needs to change operationally to align with the standard.
Lastly, create a realistic implementation plan. Define project owners, set deadlines for each phase, and build in time for review. A focused, cross-functional team ensures progress without confusion.
Step 2: Documentation (interpreting requirements, procedures)
Documenting your QMS is mandatory under the ISO 9001 standard. This isn’t about creating documents for the sake of audit — it’s about making your processes traceable, teachable, and consistent.
Begin by interpreting each clause of the standard in the context of your business. For example, Clause 8.5.1 talks about process control. For a packaging manufacturer, this could mean defining sealing temperature checks and final inspection protocols. The standard doesn’t tell you how to do it — it asks you to prove that you do.
Core documents should include:
- Quality policy and objectives
- Process maps and responsibilities
- Standard Operating Procedures (SOPs)
- Document control policies
- Risk assessments
- Corrective and preventive action procedures
Use your existing language and workflows where possible. Auditors want to see documents that teams actually use — not generic templates downloaded from the internet.
A well-structured QMS aligned with ISO 9001 requirements becomes a living system, not a filing cabinet.
Step 3: Implementation (training staff, process improvements)
Documentation only gets you halfway to compliance. You must prove that your team follows what’s written — consistently.
Start by rolling out procedures department by department. Train staff in a way that connects their daily work to the ISO 9001 requirements. For example, instead of explaining the standard’s requirement for “competence,” show how proper inspection reduces customer complaints.
Training should be documented with dates, signatures, and outcomes. Auditors will ask: “How do you ensure your operators are competent?” Your training records are the answer.
This phase also includes improving processes to reduce variation and risk. Look for bottlenecks, rework, or miscommunication. Use data from the shop floor to refine controls.
Successful implementation is visible in how people work — not just in what’s written. The end goal is operational consistency backed by evidence, which is the core of being ISO 9001 certified.
Step 4: Internal Audit (self-inspection, compliance check)
An internal audit is your rehearsal before the official evaluation. It’s also a core requirement of the ISO 9001 standard — proving you assess your own compliance regularly and act on findings.
Assign trained internal auditors, ideally from other departments. Objectivity matters. Use a checklist based on ISO clauses, but don’t limit audits to checkboxes. Review records, observe workstations, and ask staff how they apply the procedures.
Document all findings: both non-conformities and improvement opportunities. For each, assign corrective actions with deadlines and responsibilities. Follow through and retain all records.
Conduct a management review after the audit. Discuss issues raised, trends observed, and whether the QMS is achieving its goals. This review — with minutes, decisions, and follow-ups — shows leadership engagement, a key theme across ISO 9001 requirements.
By closing gaps during the internal audit phase, you significantly increase confidence ahead of the official audit.
Step 5: Certification (choosing registrar, certification audit, maintaining certification)
To demonstrate compliance, you must undergo an audit conducted by an accredited certification body. But choose carefully — the registrar’s approach can affect your experience.
Look for bodies recognized by accreditation councils (like ANAB or UKAS) and familiar with your industry. They should understand how the ISO 9001 requirements apply in your specific sector — whether that’s pharma packaging, precision tooling, or electronics assembly.
The audit itself occurs in two stages:
- Stage 1 is document review to assess readiness
- Stage 2 consists of on-site (or hybrid) audit of your QMS in action
Auditors will inspect records, interview staff, and check process consistency. If any non-conformities are found, you’ll have time to correct them. Once satisfied, the registrar issues confirmation that you’re ISO 9001 certified.
But certification is not the finish line. You’ll face annual surveillance audits and a full re-audit every three years. To stay compliant, your system must evolve with your business — through continuous internal audits, staff training, and process updates.
Meeting the ISO 9001 standard once is valuable. Sustaining it proves your system works.
Tips for a Smooth Certification Process
Plan early, document often, and involve your teams. Treat your QMS as a tool for operational clarity, not just compliance. Use root cause analysis techniques (like 5 Whys or Fishbone Diagrams) for any corrective actions. Align your QMS objectives with production KPIs — like reducing scrap, improving yield, or shortening lead time.
Use technology that supports change control, version history, and real-time visibility. This reduces audit prep time and helps you respond to findings faster.
Lastly, work with partners who understand manufacturing realities — not just theoretical compliance. The right tools and advisors make it easier to meet and maintain ISO 9001 requirements.
How BPRHub Helps Manufacturers Meet ISO 9001 Standards
Manufacturers need systems that don’t just meet ISO 9001 standards, but sustain them across years of audits, scaling, and team turnover. BPRHub provides a unified Quality, Compliance, and Governance (QCG) platform built for that exact need.
With BPRHub, your organization can:
- Centralize all QMS documents, SOPs, and quality objectives
- Automate internal audit cycles, track CAPAs, and retain audit logs
- Train staff using workflow-based documentation delivery
- Monitor compliance in real time with KPI dashboards
- Align daily operations with every clause in the ISO 9001 standard
From gap analysis to surveillance audits, BPRHub supports every phase of your compliance journey — while reducing manual work and improving visibility.
Want to get ISO 9001 certified in half the time—without drowning in spreadsheets? See how BPRHub can help
📍 Book a Demo
📧 hello@bprhub.com
Key Takeaways
→ ISO 9001 is the most widely adopted quality standard, setting clear requirements for a robust Quality Management System (QMS)
→ Getting ISO 9001 certified involves planning, documentation, implementation, internal audits, and third-party assessment
→ A thorough gap analysis provides the roadmap for aligning current practices with ISO 9001 requirements
→ Internal audits are mandatory and serve as a self-assessment tool to catch and correct issues before external review
→ ISO certification requires evidence-based documentation, staff competence, and operational consistency — not just good intentions
→ Maintaining ISO compliance involves ongoing audits, training, updates, and management reviews to ensure continuous improvement
Frequently Asked Questions
How long does ISO certification take?
The process typically takes 3 to 6 months, depending on how mature your current systems are. Smaller manufacturers with partial documentation may move faster, while larger or more complex operations often require more time to build and implement a compliant QMS aligned with all ISO 9001 requirements.
What documents are needed for ISO certification?
At minimum, your QMS must include a quality policy, quality objectives, documented procedures, process maps, training records, internal audit reports, corrective actions, and management review minutes. All documentation must be controlled and traceable per ISO 9001 standard expectations.
What is a gap analysis in ISO certification?
A gap analysis compares your current processes against the full set of ISO 9001 requirements. It identifies missing elements or weak controls in your quality system and forms the foundation of your project plan by highlighting what must be corrected before seeking external audit.
Who can issue an ISO certificate?
Only an accredited third-party certification body — often called a registrar — can issue a valid ISO certificate. The ISO organization itself does not audit or issue certificates. Accreditation must come from recognized national bodies such as ANAB or UKAS.
What is an internal audit in ISO certification?
An internal audit is a formal, documented self-check conducted to verify whether your organization’s operations comply with the ISO 9001 standard. It evaluates both documentation and practical execution, with findings used to drive corrective actions before external audit.