Quality matters in today's competitive global marketplace. It separates thriving businesses from those merely surviving. The ISO 9001 standard stands as the gold standard for quality management systems worldwide. Manufacturers rely on it to build credibility, consistency, and customer confidence.
This framework goes beyond helping you pass audits. It transforms your organization's approach to quality at every level. Pharmaceutical companies use it to ensure patient safety. Aerospace manufacturers depend on it for flight-critical components. ISO 9001 offers the structured approach needed for consistent excellence.understanding ISO 9001's seven core principles will benefit your team. Let's see how these principles can transform your manufacturing processes.
What Are The ISO 9001 Standards?
The International Organization for Standardization (ISO), 9001 represents the standard for Quality Management Systems (QMS) worldwide. Manufacturers implement these Standards to demonstrate their commitment to consistent quality and customer satisfaction. When properly applied, ISO 9001 breaks down international trade barriers while providing a systematic framework for organizational improvement.
Companies across manufacturing, healthcare, and service industries use ISO 9001 to strengthen customer trust, reduce errors, and build a culture of quality at every level. Adopting these standards supports better risk management and gives organizations a competitive edge in global markets.
Why Do Manufacturers Choose ISO 9001 Standards?
In regulated industries, compliance is more than a checkbox. For pharma and medical device manufacturers, ISO 9001:2015 Standard is the foundation for quality and trust. In the aerospace and food sectors, it’s the baseline for vendor approval and market access.
Compliance Excellence
ISO 9001 sets the global benchmark for Quality Management Systems (QMS). It’s the standard your customers, regulators, and partners expect.
Audit Readiness
Regulators and customers want proof. ISO 9001 compliance means you’re always ready-no last-minute scramble.
Operational Efficiency
When you embed the 7 quality management principles, you cut waste, reduce errors, and speed up batch release.
What ISO 9001 Compliance Actually Delivers
Compliance with ISO 9001 confirms your quality management system meets world-leading standards. Your organization earns a mark of quality that signals trust with customers and partners. Stakeholders recognize your organization as reliable and resilient, with robust processes that mitigate risk effectively.
The 7 Principles That Drive Manufacturing Excellence
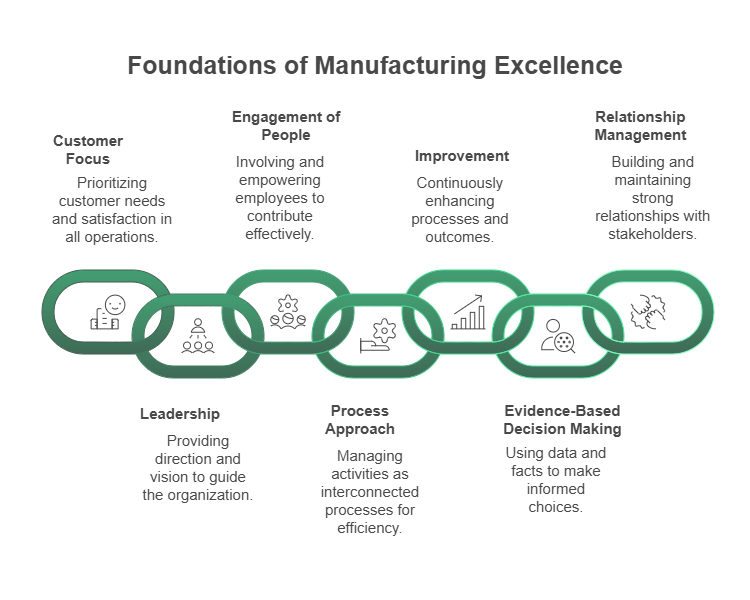
1. Customer Focus
What It Means:
Every process starts and ends with the customer’s needs.
Why It Matters:
Missed requirements mean lost contracts and recalls.
How to Operationalize:
- Map customer requirements to every SOP
- Use feedback loops to drive product and process improvements
- Track customer complaints and CAPA trends in real time
2. Leadership
What It Means:
Leaders set the tone for quality culture.
Why It Matters:
Without executive commitment, compliance slips through the cracks.
How to Operationalize:
- Make quality KPIs visible at every level
- Tie leadership reviews to audit outcomes
- Empower teams to escalate risks without fear
3. Engagement of People
What It Means:
Quality is everyone’s job-from operators to executives.
Why It Matters:
Siloed teams miss risks and opportunities.
How to Operationalize:
- Train all staff on ISO 9001 principles
- Recognize and reward proactive quality actions
- Use digital tools for easy access to procedures and records
4. Process Approach
What It Means:
Treat every activity as part of an interconnected system.
Why It Matters:
Isolated fixes don’t solve root causes.
How to Operationalize:
→ Use the Plan-Do-Check-Act (PDCA) cycle for all critical processes
- Plan processes systematically
- Do manage the processes effectively
- Check performance consistently
- Act on processes using data and information
→ Map process flows and dependencies
→ Automate handoffs to reduce manual errors
5. Improvement
What It Means:
Continuous improvement is non-negotiable.
Why It Matters:
Static systems fall behind regulatory and market changes.
How to Operationalize:
- Track nonconformances and CAPAs in a central system
- Set improvement targets and review progress quarterly
- Benchmark against industry leaders
6. Evidence-Based Decision Making
What It Means:
Decisions are driven by data, not gut feeling.
Why It Matters:
Anecdotes don’t stand up to audits.
How to Operationalize:
- Build dashboards with real-time quality metrics
- Analyze trends before issues escalate
- Document all decisions and supporting data
7. Relationship Management
What It Means:
Suppliers, partners, and customers are part of your compliance ecosystem.
Why It Matters:
A weak link can put your certification and reputation at risk.
How to Operationalize:
- Qualify and monitor suppliers using standardized criteria
- Share quality expectations and audit results transparently
- Collaborate on improvement projects
With BPRHub
- All compliance records, SOPs, and CAPAs centralized
- Automated audit trails and reminders keep you ready year-round
- Real-time dashboards for leadership and QA teams
- Supplier performance tracked and improved collaboratively
Want to see how BPRHub simplifies ISO 9001 alignment?
📍 Book a Demo
📧 hello@bprhub.com
How ISO 9001 Drives Competitive Advantage
Manufacturing organizations applying these principles have significant advantages.
Higher Customer Satisfaction
ISO 9001 Standards help align operations with customer expectations through prioritized customer focus and feedback mechanisms. Your systems identify and address customer needs, resulting in fewer product flaws.
Implementing ISO 9001 demonstrates your commitment to consistent quality. Poor quality costs manufacturers dearly, potentially affecting thousands of products and requiring expensive recalls or replacements.
Improved Operational Efficiency
Following ISO 9001 principles encourages best practices and aligns processes with quality objectives. Waste and inefficiencies decrease while continuous monitoring allows your organization to enhance efficiency and respond quickly to changes.
Manufacturing operations identify duplicated or inefficient processes through the process-based approach. Streamlining these processes frees up workforce members to focus on other tasks and boosts productivity.
Enhanced Decision Making
Collecting and analyzing reliable information enables better choices that improve operational performance and reduce risk. Evidence-based decisions lead to greater accountability and confidence in outcomes.
Manufacturing companies adopting ISO 9001 often experience a significant boost in operational efficiency, leading to an average 20% increase in profitability according to financial reports from notable industry players.
Getting Started with ISO 9001 and Implementation Checklist
Manufacturing organizations beginning their ISO 9001 journey should consider these practical steps
- Assess current operations against the seven principles
- Identify gaps in your quality management approach
- Develop an implementation roadmap prioritizing high-impact areas
- Train staff on ISO 9001 principles and their practical application
- Document processes and procedures aligned with the standard
- Conduct internal audits to verify compliance
- Make continuous improvements based on audit findings
Implementation Checklist
For QA Managers & Compliance Leaders
- Map all SOPs to the 7 quality management principles
- Centralize documentation and version control
- Automate audit scheduling and CAPA tracking
- Train staff on the ISO 9001:2015 Standard
- Benchmark KPIs and review quarterly
- Engage suppliers with clear requirements and feedback loops
Implementation requires senior management support and commitment. Leaders must understand the benefits of ISO 9001 and allocate necessary resources for implementation.
Understanding ISO 9001 requirements becomes crucial before implementation. Manufacturing teams should familiarize themselves with the standard, understand its requirements, and learn its basic structure, principles, and concepts.
Quality management systems built on ISO 9001 principles provide manufacturers with frameworks for meeting quality standards consistently. Customers emphasize product and service quality, making adherence to these principles essential for business success.
Key Takeaways
→ ISO 9001 provides a globally recognized framework for quality management systems that enhances customer satisfaction and operational efficiency
→ The seven principles (customer focus, leadership, engagement of people, process approach, improvement, evidence-based decision making, and relationship management) form the foundation of effective quality management
→ Organizations implementing ISO 9001 experience improved customer satisfaction, higher operating efficiency, and better decision-making capabilities
→ The Plan-Do-Check-Act cycle embedded in the process approach creates a systematic framework for continuous improvement
→ Leadership commitment and employee engagement are critical success factors for implementing ISO 9001 principles
→ BPRHub's platform helps organizations manage multiple quality standards simultaneously, reducing compliance risks while improving operational efficiency.
See how BPRHub simplifies ISO 9001 alignment →
📍 Book a Demo
📧 hello@bprhub.com
FAQ
What are the 7 principles of ISO 9001 and how do they help manufacturers?
The 7 principles of ISO 9001 are customer focus, leadership, engagement of people, process approach, improvement, evidence-based decision making, and relationship management-guide manufacturers to build a strong quality management system and maintain high standards.
Why do manufacturing companies follow ISO 9001 principles?
Manufacturers use ISO 9001 principles to improve product quality, meet customer expectations, and stay audit-ready. These standards also help reduce risks and drive operational efficiency.
How does the ISO 9001:2015 standard support continuous improvement?
The ISO 9001:2015 standard encourages a culture of ongoing improvement by using risk-based thinking and the Plan-Do-Check-Act cycle. This approach helps teams spot issues early and make better decisions for long-term growth.
What role does evidence-based decision making play in ISO 9001 quality management?
Evidence-based decision making, one of the 7 quality management principles, relies on data to guide actions. Manufacturers use this principle to track key metrics, address problems quickly, and support compliance with ISO 9001:2015 standard.
How can manufacturers use ISO 9001 principles to strengthen supplier relationships?
Manufacturers apply ISO 9001 principles to monitor supplier performance, set clear expectations, and collaborate on improvements. Strong supplier relationships support consistent quality and help meet all ISO 9001 requirements.