How much could a single quality misstep cost your manufacturing operation in terms of reputation, revenue, or even lives? Manufacturing leaders often ask how to maintain high quality, meet every standard, and still operate efficiently. When you’re navigating multiple standards, complex supply chains, and tight deadlines, a robust quality management system (QMS) in manufacturing isn’t just a nice-to-have-it’s a non-negotiable lifeline. According to the American Society for Quality (ASQ), Companies with mature QMS achieve an average on-time delivery rate of 92%, compared to just 74% for those without mature systems. This significant 18% difference highlights how QMS streamlines processes to ensure timely production and delivery. A well-implemented QMS ensures your team is audit-ready, minimizes nonconformance, and empowers you to scale with unshakable confidence.
What is a Quality Management System (QMS) in Manufacturing?
A QMS in manufacturing isn’t just a set of rules-it’s the backbone of reliable production. It weaves together every process, procedure, and responsibility so quality isn’t left to chance. From planning to final checks, a QMS keeps every stage in sync, making sure nothing slips through the cracks.
The real purpose is to drive quality up and defects down, all while staying ahead of regulations like ISO 9001, Food and Drug Administration, and GMP. With a QMS, compliance stops being a headache and becomes an advantage. It’s how manufacturers build trust, scale up safely, and turn quality into a strength-not just a requirement.
Why Do Manufacturers Need a QMS?
Quality can’t be left to chance. When teams rely on memory or scattered documents, mistakes slip through. A QMS for manufacturing brings order. It defines every step, from raw material checks to final inspections. Everyone knows their role. Every process is documented. If a deviation happens, it’s flagged and tracked until resolved.
A strong QMS also makes audit readiness part of daily work. Documentation is always up to date. Nonconformance reporting is quick and clear. Teams can show compliance at a moment’s notice, not just scramble when an audit looms.
QMS Benefits Table
Benefit Impact on Manufacturing
Core Elements of a Manufacturing QMS
A QMS in manufacturing is built on a few key pillars,
Quality Policy and Objectives
A manufacturing QMS stands on a set of essential pillars that bring structure and clarity to quality management. It starts with a clear quality policy and objectives-leadership defines the vision, setting measurable goals that guide every process and decision.
Documented Procedures
Standardized, documented procedures are the backbone. These SOPs ensure that every task, from material handling to final inspection, is done the same way each time. No guesswork. Everyone follows the same playbook.
Training and Competency
Training is woven in. Employees aren’t just told what to do-they’re shown how to do it right. Regular training keeps skills sharp and expectations clear, reducing errors and building confidence.
Monitoring and Audits
Monitoring and audits are routine, not afterthoughts. Regular checks-whether inspections, process audits, or data reviews-catch issues early, before they snowball. Audit trails and records keep everything transparent and traceable.
Nonconformance Reporting (NCR)
Nonconformance reporting (NCR) is built in. Every deviation from the standard is logged, flagged, and tracked, nothing slips through the cracks. Each issue becomes a chance to learn and improve, not just a box to check.
Corrective and Preventive Actions (CAPA)
Corrective and preventive actions (CAPA) go deeper. Problems aren’t just patched-they’re traced to the root cause and fixed for good. Preventive steps are taken to stop similar issues before they start.
Continuous Improvement
Continuous improvement is the culture. Teams use data, feedback, and lessons learned to refine processes. The QMS isn’t static-it evolves, driving efficiency, reducing waste, and raising the bar for quality every day.
Equipment Management
A robust QMS also extends to equipment management. Equipment is maintained and calibrated on schedule, minimizing downtime and defects.
Change Control
Changes to processes or products are controlled and documented, preventing surprises and ensuring consistency.
Supplier Oversight
Suppliers are monitored to ensure the quality of incoming materials matches your standards.In short: a manufacturing QMS is more than a checklist. It’s a living system that connects people, processes, and technology-making quality to everyone's responsibility, every day.
Read more→ Understanding the 7 Principles of ISO 9001: A Comprehensive Guide
The QMS Process: Step by Step
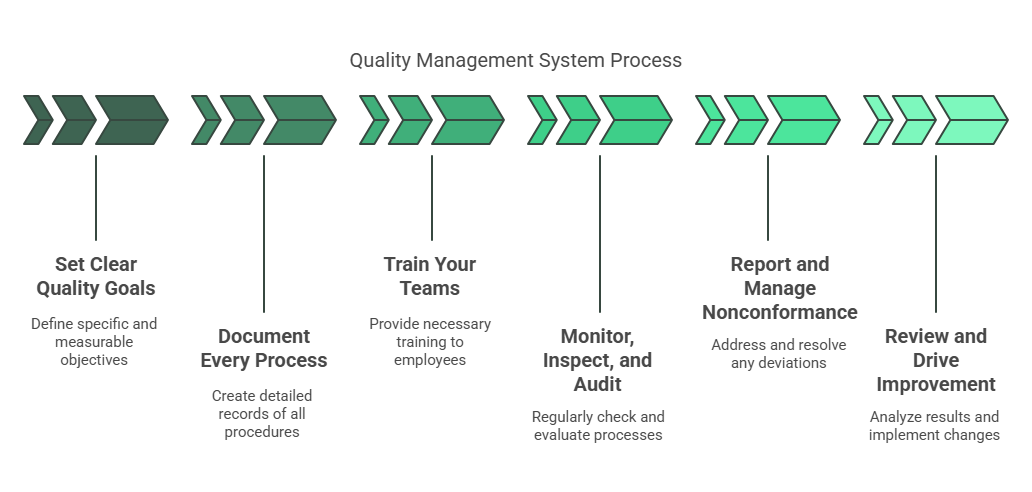
Step 1 Set Clear Quality Goals
Start by defining what quality means for your operation. Establish a quality policy and set measurable objectives that align with customer and regulatory expectations. These goals become the foundation for all quality activities.
Step 2 Document Every Process
Write down each critical process, procedure, and work instruction. This includes creating a quality manual, standard operating procedures (SOPs), and checklists to ensure everyone follows the same path from raw material handling to finished product inspection. Effective document control keeps these records current and accessible.
Step 3 Train Your Teams
Make sure every employee understands their role and the documented procedures. Training ensures consistency and builds a culture where quality is everyone’s responsibility. Training records should be maintained and regularly updated.
Step 4 Monitor, Inspect, and Audit
Use checklists, spot checks, and both internal and external audits to verify compliance. Regular inspections and process audits catch deviations early and ensure that standards are met on the shop floor. Data from these activities is tracked for trends.
Step 5 Report and Manage Nonconformance
When something goes wrong, log the deviation immediately. Investigate the root cause using tools like the 5 Whys or fishbone diagrams. Then, implement corrective and preventive actions (CAPA) to address the issue and stop it from recurring. Every step is documented for traceability.
Step 6 Review and Drive Improvement
Analyze audit findings, production data, and customer feedback to spot opportunities for refinement. Use continuous improvement methods-like the Plan-Do-Check-Act (PDCA) cycle-to make targeted changes and raise quality standards over time. Management reviews these results and sets new objectives as needed.
With BPRHub:
All compliance data lives in one place. BPRHub keeps you ready year-round. Nonconformance reporting and deviation management are automated. Dashboards provide real-time visibility. Teams spend less time on paperwork and more time on production. Audit findings drop, and growth speeds up.
Ready to streamline compliance and boost quality with ease? See how BPRHub keeps you audit-ready and focused on growth. Book a demo now!
📍 Book a Demo
📧 hello@bprhub.com
QMS in Pharma: Raising the Bar
Pharmaceutical manufacturing leaves no room for error. QMS in pharma must meet strict standards like Current Good Manufacturing Practice (CGMP) and FDA requirements. Every batch is tracked. Every deviation is documented and investigated. Audit readiness is non-negotiable. Deviation management is systematic-issues are identified, root causes analyzed, and preventive actions put in place.
Pharma QMS also emphasizes:
Batch Manufacturing Records (BMRs): Every step is logged for traceability.
Change Control: Any process change is reviewed and approved.
Product Quality Reviews: Regular analysis ensures ongoing compliance.
Real Business Benefits of a QMS
- Audit Preparedness: Be ready for any audit, any time.
- Reduced Nonconformance: Fewer defects mean less waste and lower costs.
- Faster Deviation Management: Issues are resolved quickly, preventing bigger problems.
- Better Compliance: Stay aligned with ISO 9001, FDA, and other standards-opening new markets.
- Stronger Supplier Management: Track vendor quality and performance.
- Data-Driven Decisions: Dashboards and reports highlight trends and risks.
Integrating QMS with Technology: The Manufacturing Advantage
Paper-based systems can’t keep pace with today’s manufacturing demands. Integrating a QMS with digital tools transforms operations. ERP connections sync quality data with production and inventory, keeping workflows smooth and unified. Real-time dashboards offer instant clarity-teams see metrics, spot deviations, and monitor supplier health as issues emerge. Automated compliance workflows cut manual errors and make audit prep routine, not a scramble.
These tools make audit readiness routine. Manufacturers can focus less on paperwork and more on innovation and growth, knowing compliance and quality are always in check.
QMS as a Growth Engine: Governance for Business Success
Quality management isn’t just about avoiding penalties-it’s a driver for business growth. A robust QMS helps manufacturers
- Enter new markets quickly by demonstrating global compliance
- Unlock revenue by reducing downtime and defects through standardized processes
- Scale confidently with risk mitigation and continuous improvement built in
By leveraging modern QMS platforms, manufacturers gain more than compliance, they build a foundation for sustainable growth, operational excellence, and a reputation for quality that opens new opportunities. A digital QMS doesn’t just keep you compliant. It keeps you competitive.
See How BPRHub Solves the Problem
Ready to move faster, reduce risk, and stay audit-ready year-round? BPRHub centralizes your QMS for manufacturing, automates compliance with ISO, FDA, and other standards, and gives you real-time insights to drive improvement.
A well-run QMS for manufacturing is more than a checklist. It’s your engine for reliable quality, audit readiness, and business growth. Don’t let compliance slow you down-let it drive you forward.
Need help mapping with QMS to your current systems? Talk to BPRHub compliance experts.
📍 Book a Demo
📧 hello@bprhub.com
Key Takeaways
→ A quality management system in manufacturing sets clear processes so teams can deliver consistent, compliant products every time.
→ Audit preparedness, nonconformance reporting, and deviation management are built into a strong QMS, reducing risks and surprises.
→ Adopting a QMS for manufacturing streamlines compliance with ISO, FDA, and other standards, making it easier to expand or enter new markets.
→ Data-driven insights from a QMS help you spot issues early and drive continuous improvement across your operations.
→ QMS in pharma manufacturing brings extra rigor, ensuring every batch meets strict safety and regulatory demands.
→ BPRHub unifies compliance, automates documentation, and keeps you audit-ready-so you can focus on growth, not paperwork.
FAQ
What is a quality management system in manufacturing?
Quality in manufacturing can’t be left to guesswork. A quality management system (QMS) brings structure and clarity. It lays out every process and responsibility, from document control to training, ensuring that nothing slips through the cracks. With a QMS, every product batch is tracked and meets standards like ISO 9001. Teams know exactly what’s expected, and every step is documented-so quality isn’t just a goal, it’s a guarantee.
How does a QMS for manufacturing improve audit preparedness?
Audits shouldn’t be a scramble. A QMS keeps compliance documents, records, and procedures organized and always current. When an audit comes, everything you need is at your fingertips. Digital QMS solutions with features like Audit Hub make it easy to find and share information instantly. Instead of dreading audits, teams handle them as part of daily business-no stress, no last-minute rush.
Why is nonconformance reporting important in a QMS process?
Catching problems early is key to quality. Nonconformance reporting in a QMS ensures that every issue-no matter how small-is logged and tracked. When a deviation happens, it’s recorded, assigned for follow-up, and resolved with clear documentation. This stops mistakes from repeating and drives continuous improvement. If a part fails inspection, the QMS makes sure the fix is documented and the lesson is learned.
What makes QMS in pharma different from other industries?
Pharmaceutical quality is about more than just product-it’s about patient safety. QMS in pharma is built to meet tough standards like FDA and GMP. Every step, from batch records to deviation tracking, is tightly controlled and documented. This rigorous approach helps pharma companies avoid costly recalls and stay compliant worldwide, protecting both patients and reputation.
How does a digital QMS platform help manufacturers scale operations?
Growth shouldn’t mean losing control. A digital QMS automates routine tasks-like document management, training, and supplier oversight-so teams can focus on what matters. Real-time dashboards and automated workflows cut down on manual errors and speed up compliance. As manufacturers add new lines or sites, quality stays consistent and compliance risks stay low. Scaling up becomes smooth and secure.