Quality cannot be left to chance in manufacturing. Teams relying on memory or scattered documents often make mistakes. A Quality Management System (QMS) for manufacturing brings order. Quality becomes a strategic advantage that drives customer loyalty, reduces costs, and builds a strong market reputation.
Many manufacturers face challenges with the basics of quality management. The difference between quality assurance and quality control is fundamental. Operational efficiency, compliance, and profitability depend on understanding both. Manufacturers who balance quality assurance and quality control create a framework for excellence. Knowing how these disciplines work together protects product integrity and drives improvement.
The Strategic Difference: Prevention vs. Detection
Quality assurance and quality control serve different functions. Both aim to deliver high-quality products.
Quality assurance (QA) uses a proactive and process-oriented approach. QA prevents defects before they occur. Systematic activities and procedures during product development ensure quality is built into every process.
Quality control (QC) uses a reactive and product-oriented approach. QC identifies defects after they occur. Inspection, measurement, and testing confirm that products meet quality standards before reaching customers.
A QMS defines every step. Raw material checks and final inspections are part of the process where every role is clear. Documentation covers every process, deviations are flagged and tracked until resolved. Audit readiness becomes part of daily work and documentation stays current. Nonconformance reporting is quick and clear where teams can show compliance at any time.
With BPR Hub.
Quality assurance processes and quality control checkpoints unite in one platform, creating a seamless quality management workflow that prevents issues proactively while maintaining robust inspection protocols.
Read more about → ISO Certification Process for Manufacturers: Step-by-Step Guide for Manufacturers
Key Differences That Impact Your Operations
Understanding the quality assurance and quality control difference, helps you build more effective quality management systems:
Quality Assurance in Action: Building Quality Into Your Processes
Quality assurance uses several key activities.
- Plan quality objectives and requirements for manufacturing.
- Design, Develop and use quality controls during product design.
- Process Implementation for procedures and guidelines to be consistent.
- Keep detailed records and share them.
- Use data and feedback for continuous improvement..
Manufacturers may use Good Manufacturing Practices (GMP) for Standard operating procedures (SOPs), Internal audits that are conducted regularly and a comprehensive documentation system to support every process.
Quality Control in Practice: Verifying Product Excellence
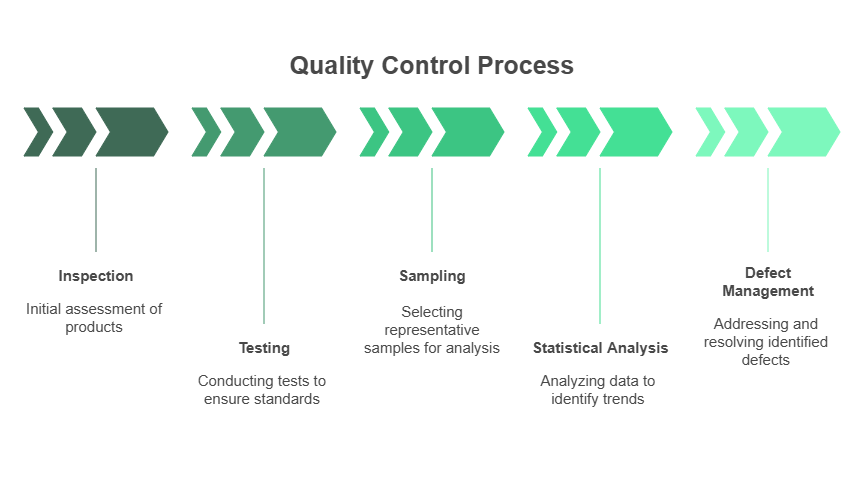
Quality control uses specific verification activities.
- Examine products visually or with tools to find defects.
- Check product performance against specifications.
- Select products from batches for quality checks.
- Use data to find trends and quality issues.
- Address and resolve quality problems.
Manufacturers use in-process inspections, final product testing, statistical sampling, and non-conformance management.
Industry-Specific Applications: Where QA and QC Matter Most
The difference between QA and QC appears clearly in different industries.
Pharmaceutical Manufacturing
Quality assurance in pharmaceuticals means following Good Manufacturing Practices (GMP), validating every production step, and keeping thorough documentation. Quality control means testing each drug batch for potency, purity, and stability before release. Strict rules apply. FDA regulations and ICH Q10 guide every process. A pharmaceutical QMS keeps everything organized with a clear hierarchy of documents. Every role is clear, every process is documented. Problems are flagged and tracked until fixed. Teams stay compliant every day.
Medical Devices Industry
Quality assurance focuses on risk management and hazard analysis throughout the product lifecycle. Quality control uses strict testing protocols and validation. Device safety and efficacy are ensured. ISO 13485 sets the standard for QA in this field.
General Manufacturing
Quality assurance and quality control follow ISO 9001:2015 standards. These standards specify requirements for a quality management system. Companies provide products that meet customer and regulatory needs. A manufacturing QMS includes documented information, planning, management review, design, monitoring, and improvement.
Ready to unify quality assurance and quality control for manufacturing excellence? Book a demo with BPRHub today!
📍 Book a Demo
📧 hello@bprhub.com
Balancing QA and QC for Operational Excellence
Successful manufacturers use both QA and QC.
- Unified Quality Framework. Build a system that includes QA and QC.
- Risk-Based Approach. Allocate resources based on product risk and complexity.
- Data-Driven Decision Making. Use metrics from QA and QC to improve.
- Technology Integration. Use digital tools to connect QA and QC.
What Goes Wrong When QA and QC Are Siloed
Separating quality assurance and quality control into disconnected functions creates serious risks for manufacturers. Without collaboration, critical information is missed, and the consequences impact compliance, cost, and customer trust.
Audit failures happen when QA and QC teams use different systems or don’t align, audit trails become incomplete or inconsistent. Missing documentation, unresolved deviations, and unclear responsibilities can lead to failed inspections or regulatory penalties.
Recall Risks increase if QA doesn’t receive timely feedback from QC, systemic issues go unnoticed. Defects may pass through unchecked, increasing the chance of product recalls that damage reputation and profitability.
Duplicated Efforts, siloed teams often create overlapping documentation, redundant inspections, and inconsistent procedures. This wastes time and resources, making it harder to scale operations efficiently.
Miscommunication may happen when QA and QC don’t share a unified platform or workflow, teams may misunderstand requirements or miss updates. This breakdown in communication delays decision-making and weakens response to quality issues.
Missing Improvement Opportunities, in which valuable QC insights may never reach QA teams, limiting the ability to refine processes and prevent future issues. Continuous improvement efforts suffer when feedback loops are broken.
Integrating QA and QC within a single quality management system ensures transparency, accountability, and coordination. Teams work with shared goals, accurate data, and aligned processes to drive manufacturing excellence.
Transforming Quality Management with Digital Solutions
Manufacturers use technology to connect QA and QC.
- Centralized documentation to store all quality documents in one place.
- Real-Time quality monitoring for tracking metrics for QA and QC.
- Automated workflow for providing a streamline process from design to inspection.
- Integrated compliance management for following multiple standards in one system.
How BPRHub Can Help and Why Companies Benefit
BPRHub offers a unified platform for Quality, Compliance, and Governance. Manufacturers can integrate quality assurance and quality control by
- Documentation hub to store all documents, SOPs, and records in one searchable place.
- Audit hub to stay audit-ready with automated compliance tracking.
- Deviation management to track and resolve quality issues with CAPA workflows.
- Real-Time analytics for monitoring quality metrics for QA and QC.
BPRHub supports manufacturers in improving quality management. The platform reduces the divide between QA and QC. Both disciplines keep their strengths. Risk is reduced. Compliance improves. Audit readiness is always maintained.
Book a demo or contact a compliance expert to see how BPRHub can support your quality management goals.
📍 Book a Demo
📧 hello@bprhub.com
Key Takeaways
→ Quality assurance works proactively and focuses on processes. Defects are prevented through systematic activities and procedures implemented before production.
→ Quality control operates reactively and focuses on products. Defects are detected through inspection and testing after production.
→ The difference between QA and QC is in timing, focus, and approach.
→ Effective quality management uses both QA and QC as complementary disciplines.
→ QA and QC have different roles in pharmaceutical, medical device, and general manufacturing.
→ Digital solutions like BPRHub connect QA and QC in one system.
FAQ
What is the main difference between quality assurance and quality control?
Quality assurance works proactively and focuses on processes. Defects are prevented by establishing systematic procedures before production. Quality control operates reactively and focuses on products. Defects are found through inspection and testing after production. QA builds quality into processes. QC checks if products meet requirements.
How do quality assurance and quality control work together?
Quality assurance and quality control are both parts of a quality management system. QA sets the processes and standards. QC checks if these work by inspecting products. QA prevents issues. QC finds any that occur. QC results help improve QA.
What are examples of quality assurance activities in manufacturing?
QA activities include creating SOPs, using GMP, validating processes, training employees, auditing, keeping records, and managing changes. These activities prevent quality issues by ensuring consistency.
What are examples of quality control activities in manufacturing?
QC activities include inspections, testing, measurements, sampling, lab analysis, and reporting non-conformance. QC teams use these activities to check if products meet requirements before shipping.
How can a digital QMS help balance quality assurance and quality control?
A digital QMS gives teams one platform for both QA and QC. Documents are stored, workflows are automated, quality is monitored, non-conformance is tracked, and analytics are provided. QC insights help improve QA. Quality keeps improving through this closed-loop system.
What standards govern quality assurance and quality control in different industries?
General manufacturing uses ISO 9001:2015. Pharmaceutical manufacturing follows FDA, EU GMP, ICH Q10, and PIC/S. Medical device makers use ISO 13485. Aerospace companies use AS9100D. These standards set rules for QA and QC in each industry.