Do you struggle with inventory issues, order inaccuracies, or customer dissatisfaction? Are your warehouse operations aligned with ISO 9001 warehouse standards and globally recognized quality management principles? Implementing ISO 9001 in your warehouse can streamline your processes, boost operational efficiency, and enhance customer satisfaction.
In fact, an estimated 2.1 million companies worldwide are ISO 9001 certified, spanning over 170 countries. These certifications are continually updated to align with the latest best practices in quality management, ensuring that organizations stay at the forefront of quality assurance.
This guide will take you through the critical steps of applying ISO 9001 to warehouse management, helping you set up an effective Quality Management System (QMS), optimize resource management, and control processes, and continuously improve operations.
Why ISO 9001 Matters for Warehouses?
ISO 9001 offers a structured approach to quality management, helping warehouses streamline operations, reduce errors, and improve customer satisfaction. Here’s how it benefits warehouses:
- Efficient Workflows and Process Improvement: Standardizing our procedures ensures seamless coordination across all teams, from drivers to warehouse staff. ISO 9001 standardizes supply chain operations, promoting consistency, predictability, and repeatability. This reduces variability, improves service quality, and minimizes errors.
- Inventory Accuracy: ISO 9001 ensures accurate inventory tracking and traceability, minimizing errors in stock levels, reducing discrepancies, and enhancing order fulfillment.
- Improves Customer Satisfaction: By improving order accuracy and delivery timelines, ISO 9001 boosts customer satisfaction, fostering loyalty and long-term relationships.
- Regulatory Compliance: ISO 9001 helps warehouses stay compliant with industry regulations by maintaining thorough documentation, and ensuring legal and regulatory requirements are met. Also, warehousing and logistics companies are required to adhere to multiple regulatory standards, including safety and environmental guidelines.
- Streamlines Inventory Management: Space is valuable in warehousing. By applying ISO 9001 principles, we reduce waste, optimize space, and improve inventory management.
Implementing ISO 9001 elevates warehouse operations, enhancing efficiency, quality, and compliance while improving customer trust.
How Can You Optimize the Warehouse Process Flow?
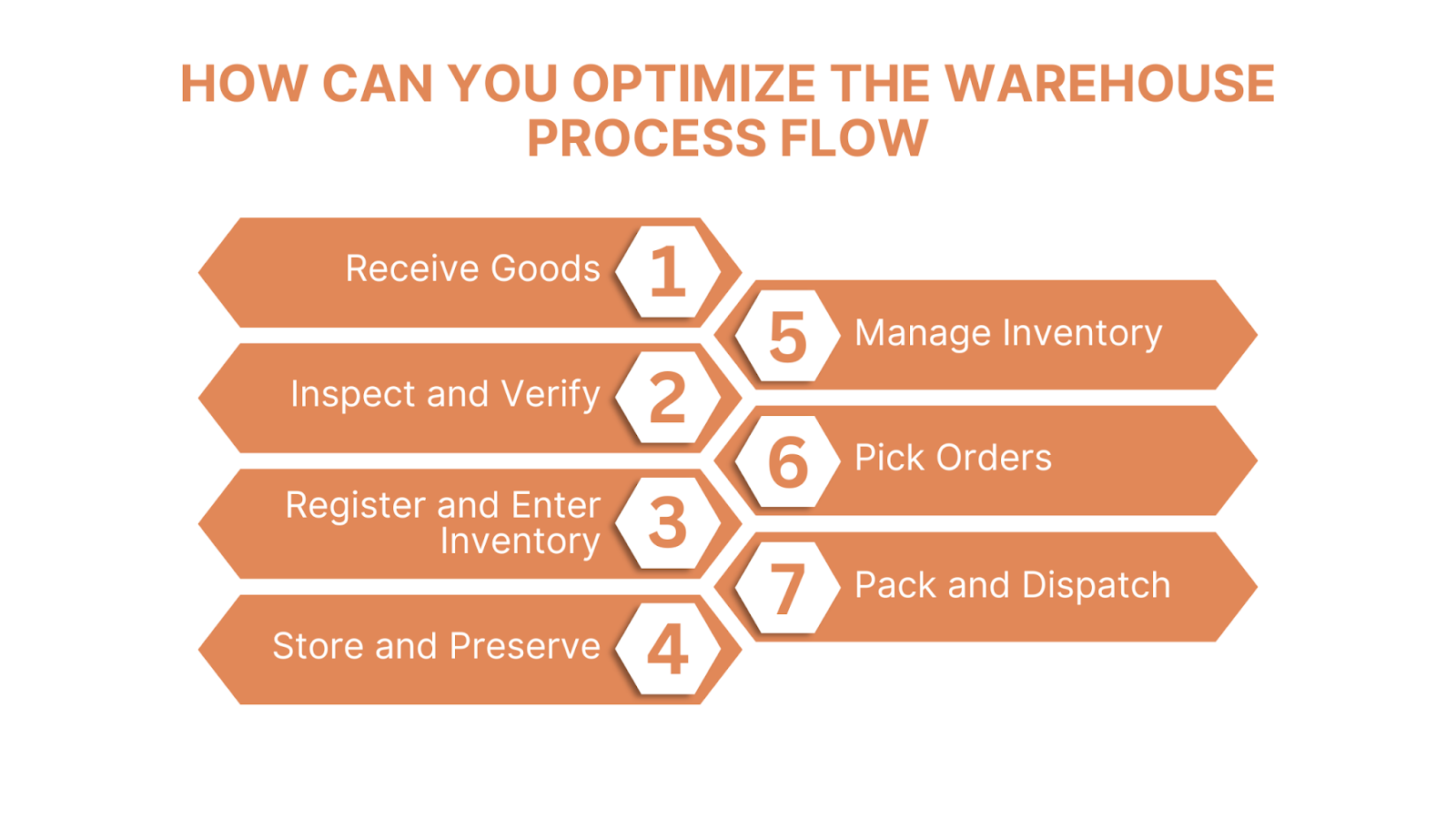
Before diving into ISO 9001 requirements, it’s essential to map a warehouse’s operational flow. This step identifies areas where ISO 9001 can drive improvements. Here's a typical workflow.
- Receive Goods – Unload shipments, verify delivery documentation, and inspect the condition of items.
- Inspect and Verify – Check for damages, quality, and compliance with order specifications.
- Register and Enter Inventory – Record approved items in the warehouse management system for traceability.
- Store and Preserve – Use appropriate storage solutions and environmental controls.
- Manage Inventory – Monitor stock levels, conduct cycle counts, and prevent discrepancies.
- Pick Orders – Retrieve accurate items for orders, ensuring precise selection.
- Pack and Dispatch – Package items securely, prepare documentation, and update inventory records.
By understanding the operational flow, you can better align warehouse activities with the ISO 9001 standards. Now, let’s explore how the key ISO 9001 requirements map to each stage of this process to ensure seamless and efficient operations.
Key ISO 9001 Requirements Mapped to Warehouse Processes
Understanding how ISO 9001 applies to each stage of warehouse operations helps ensure effective quality management. The following mapping illustrates the key clauses linked to warehouse processes and how they can optimize efficiency and accuracy.
1. Receive Goods
- Clause 8.4.1: Verify supplier compliance with specified requirements.
- Clause 8.5.2: Ensure traceability from receipt through storage.
- Clause 8.5.3 – Property Belonging to Customers or External Providers: Ensure customer or supplier goods are properly received, handled, identified, and protected.
2. Inspect and Verify
- Clause 8.6: Validate acceptance criteria before adding items to inventory.
- Clause 7.1.5: Calibrate and maintain inspection tools for accuracy.
- Clause 8.5.1 – Control of Production and Service Provision: Control processes to ensure products meet specifications during inspection.
- Clause 8.7 – Control of Nonconforming Outputs: Identify and manage nonconforming goods during inspection, segregating them to prevent unintended use.
- Clause 8.5.3 – Property Belonging to Customers or External Providers: Report and record incidents of lost, damaged, or unsuitable customer-owned property.
- Clause 10.2 – Nonconformity and Corrective Action: Implement corrective actions to address and resolve nonconformities.
- Clause 7.5 – Documented Information: Maintain records of inspections, non-conformities, and their resolution.
- Clause 8.5.2 – Identification and Traceability: Ensure inspection status and results are clearly identified and traceable.
3. Register and Enter the Inventory
- Clause 7.1.3: Maintain infrastructure supporting inventory systems.
- Clause 7.5: Ensure proper documentation for traceability.
- Clause 8.5.2 – Identification and Traceability: Assign product identification for traceability in the inventory system.
4. Segregate and treat non-conforming items
- Clause 7.5 – Documented Information: Maintain records of nonconformities and their resolution.
- Clause 8.5.3 – Property Belonging to Customers or External Providers: Report and record any lost, damaged, or unsuitable customer-owned property.
- Clause 8.7 – Control of Nonconforming Outputs: Segregate nonconforming products to prevent unintended use.
- Clause 10.2 – Nonconformity and Corrective Action: Implement actions to address and correct nonconformities.
5. Store and Preserve
- Clause 8.5.4: Preserve product quality with adequate storage conditions.
- Clause 7.1.4: Provide controlled environments for sensitive items.
- Clause 7.1.3 – Infrastructure: Ensure infrastructure for storage and handling (e.g., shelving, climate control, forklifts).
6. Manage Inventory
- Clause 9.1: Monitor inventory for performance evaluation.
- Clause 7.1.5: Use calibrated tools to ensure inventory accuracy.
- Clause 8.5.4 – Preservation: Manage inventory to prevent deterioration and maintain product conformity.
- Clause 7.1.4 – Environment for Process Operations: Provide an environment that supports accurate inventory management.
7. Pick Orders
- Clause 8.5.1: Control processes to ensure correct order fulfillment.
- Clause 8.5.2: Maintain traceability throughout the picking process.
- Clause 7.1.4 – Environment for Process Operations: Ensure the picking area supports efficient, error-free operations.
8. Pack and Dispatch
- Clause 8.5.4: Use appropriate packaging to protect items during transit.
- Clause 7.5: Document shipping details and maintain records.
- Clause 8.6 – Release of Products and Services: Verify product compliance before dispatch.
- Clause 8.2.1 – Customer Communication: Provide customers with delivery details and documentation.
Other Requirements for a Warehouse:
- Clause 5.3 – Organizational Roles, Responsibilities, and Authorities: Clearly define and communicate roles and responsibilities within the warehouse.
- Clause 7.1.2 – People: Ensure the warehouse is staffed with qualified personnel to operate efficiently.
- Clause 7.1.3 – Infrastructure: Provide the necessary physical resources for smooth operations, maintaining facilities and equipment to avoid disruptions. Invest in infrastructure that boosts productivity and safety.
- Clause 7.1.6 – Organizational Knowledge: Identify and retain critical knowledge required for warehouse operations.
- Clause 7.2 – Competence: Ensure employees are competent based on their education, training, skills, and experience.
- Clause 7.3 – Awareness: Ensure employees understand the quality policy, objectives, and their role in achieving them. Make staff aware of how their actions impact product quality and customer satisfaction.
- Clause 7.5 – Documented Information: Maintain and control necessary documentation, ensuring it is accurate and up-to-date to guide warehouse operations. Keep records to demonstrate compliance and effective operation of the QMS.
This emphasis on packaging and documentation sets the stage for improving overall warehouse performance. By utilizing ISO 9001 data effectively, warehouses can address gaps and refine processes for greater efficiency.
Discover how BPRHub expert guidance can help you implement ISO 9001 warehouse standards effectively and bring value to your business. Get in touch with us today!
Leveraging ISO 9001 Data to Optimize Warehouse Performance
Implementing ISO 9001 is not just about compliance—it's about improving efficiency and streamlining processes. Here’s how you can use the data to optimize warehouse operations:
Key Strategies for Data-Driven Warehouse Optimization
- Workforce Training & Competence (Clause 7.2): Ensure employees receive continuous training to develop the necessary skills, minimize errors, and enhance overall productivity. Well-trained staff contribute to a more efficient and error-free warehouse environment.
- Accurate Documentation & Record-Keeping (Clause 7.5): Maintain detailed and up-to-date records to support audits, improve traceability, and ensure smooth operational workflows. Proper documentation helps in identifying process gaps and implementing corrective actions.
- Infrastructure & Technology Investments (Clause 7.1.3): Upgrade warehouse facilities, invest in automation tools, and optimize layouts to improve safety, workflow efficiency, and resource utilization. A well-structured infrastructure minimizes operational bottlenecks and enhances productivity.
- Commitment to Continuous Improvement (Clause 10.2): Adopt a proactive approach to identifying and addressing nonconformities. Regularly review processes, gather performance data, and implement corrective actions to adapt to evolving business needs and maintain high-quality standards.
By harnessing these ISO 9001-driven strategies, warehouses can boost efficiency, reduce operational risks, and elevate customer satisfaction—turning compliance into a powerful tool for business growth.
Key Benefits of Implementing ISO 9001 in Warehouses
Adopting ISO 9001 standards can bring significant improvements to warehouse operations, including:
- Boosted Customer Satisfaction: Accurate inventory management and reliable delivery enhance customer trust and satisfaction.
- Streamlined Operations: Standardized workflows reduce inefficiencies, saving time and resources.
- Fewer Errors: Rigorous quality checks and inventory controls minimize mistakes in picking, packing, and shipping.
- Engaged Workforce: Clear role definitions and regular training foster a motivated and efficient team.
ISO 9001 not only establishes a foundation for quality but also empowers warehouses to continuously improve their operations. One key area where this plays out is in the management of inventory, audits, and ongoing process refinement.
How Can Inventory Management & Continuous Improvement Drive ISO 9001 Success?
Effective inventory management, regular audits, and continuous improvement are essential for maintaining ISO 9001 compliance in warehouse operations.
- Managing Inventory Efficiently: Effective inventory management is a critical component of ISO 9001 warehouse standards. This includes using inventory management software, conducting regular stock counts, and monitoring inventory levels to prevent both stockouts and excess inventory.
- Regular Inventory Audits for Accurate Tracking: ISO 9001 requires warehouses to implement systematic auditing of inventory. Regular audits ensure that stock discrepancies are identified and corrected in a timely manner, maintaining inventory accuracy and consistency.
- Dealing with Inventory Discrepancies and Non-Conformities: Though discrepancies are inevitable, ISO 9001 mandates that warehouses have a clear process for addressing them. Non-conformities should be promptly managed, with corrective actions taken to prevent their recurrence.
- Comprehensive Audits and Continual Improvement: Conducting regular audits is essential for compliance with ISO 9001. These audits should encompass all aspects of warehouse operations—especially inventory management and quality processes. The findings should be used to pinpoint inefficiencies and areas for improvement.
- Utilizing Data for Gap Identification and Process Refinement: ISO 9001 encourages warehouses to assess their operations against the standard to identify gaps regularly. Analyzing these gaps helps in improving training, system documentation, and supply chain processes, which ultimately enhances compliance and efficiency.
By continuously refining these processes, warehouses can ensure they meet ISO 9001 standards and optimize their operations.
Want to Streamline your Warehouse Processes and Ensure ISO 9001 Compliance?
At BPRHub, we specialize in providing expert solutions that make implementing ISO 9001 warehouse standards seamless and efficient. Whether it’s optimizing your processes, ensuring comprehensive training, conducting audits, or improving system documentation, we equip you with the right tools to maintain a compliant and high-performing warehouse.
With BPRHub, you can ensure that your warehouse is consistently meeting ISO 9001 standards, boosting efficiency, reducing errors, and improving customer satisfaction.
FAQs
1. What are ISO 9001 warehouse standards?
ISO 9001 warehouse standards provide a framework for implementing a Quality Management System (QMS) in warehouse operations, ensuring efficiency, accuracy, and customer satisfaction.
2. How do ISO 9001 standards help minimize errors in warehouses?
These standards emphasize quality checks, traceability, and robust inventory control systems to reduce errors in receiving, picking, packing, and shipping processes.
3. What are the benefits of implementing ISO 9001 warehouse standards?
Benefits include improved customer satisfaction, operational efficiency, reduced errors, engaged employees, and a stronger competitive edge in the supply chain.
4. What key processes in warehouses are aligned with ISO 9001 standards?
Processes such as receiving goods, inspection, inventory management, storage, order picking, packing, and dispatch are all optimized under ISO 9001 warehouse standards.
5. How can ISO 9001 warehouse standards improve operational efficiency?
By standardizing workflows, reducing waste, and establishing clear guidelines for processes like inventory management, order picking, and shipping, ISO 9001 helps streamline operations and save costs.