Manufacturing leaders often ask whether implementing environmental management systems is a legal requirement or a strategic choice. The answer might surprise you-and open new doors for competitive advantage. Most regions do not make ISO 14001 mandatory by law, but market pressures and government contracts often push organizations to adopt the standard.
Companies that follow ISO 14001 show a strong commitment to environmental responsibility, gain an edge in competitive bids, and build trust with customers who value sustainability. Choosing to implement this standard opens opportunities for cost savings, risk reduction, and easier access to new markets.
The Truth About ISO 14001 Requirements
The International Organization for Standardization (ISO), 14001 is not legally mandatory in most regions worldwide. Organizations voluntarily adopt this Standard to showcase their environmental commitment and improve performance. While the standard itself remains optional, certain circumstances might make implementation necessary:
- Government contracts often require suppliers to maintain an environmental management system
- Industry-specific regulations may effectively mandate ISO 14001 compliance
- Market pressures from environmentally conscious customers can make the standard a practical necessity
What Documentation Is Required for ISO 14001?
To get ISO 14001 compliance, your organization must provide documented evidence that your Environmental Management System (EMS) adheres to established standards. Key documentation includes
- Scope of the EMS defining operational boundaries and covered processes
- Environmental policy statement showing your commitments and goals
- List of interested parties and their requirements
- Documented information on environmental aspects and impacts
- Operational control procedures for managing environmental aspects
- Emergency preparedness and response procedures
- Records of monitoring and measurement activities
The standard allows flexibility in documentation methods while ensuring effective environmental processes are in place and verifiable.
Why Manufacturers Choose ISO 14001
Manufacturing leaders see ISO 14001 not as a regulatory burden but as a strategic advantage. The standard provides a framework for
- Identifying environmental risks before they become costly problems
- Streamlining resource usage to cut operational expenses
- Building credibility with customers who demand environmental responsibility
- Opening doors to new markets with strict environmental requirements
Key Benefits of ISO 14001 Implementation
1. Lower Operating Costs
ISO 14001 helps you run leaner. It pushes you to find efficiencies across your operations—like cutting energy use on the production floor, using raw materials more wisely, and managing waste in ways that reduce disposal costs. Even water usage can drop with smarter recycling and conservation.
2. A Stronger Position in the Market
Environmental performance matters more than ever to buyers. ISO 14001 helps your business stand out, especially when competitors can’t show the same level of commitment. It can also open doors to big customers with strict supplier requirements, help you qualify for government contracts, and build trust with customers who care about sustainability.
3. Better Control Over Risk and Compliance
Environmental regulations aren’t getting any simpler. ISO 14001 gives you a clear framework to stay ahead—spotting legal requirements early, tracking changes that could impact your operations, and keeping documentation ready for audits. That means fewer surprises, lower risk of fines, and less disruption to your business.
Steps to ISO 14001 Implementation
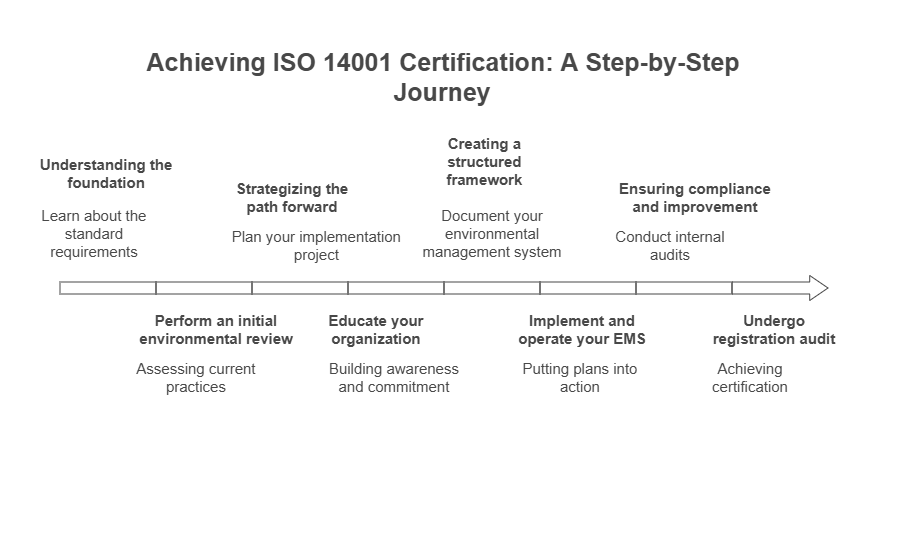
Step #1: Learn about the standard requirements
ISO 14001 contains specific clauses covering leadership, planning, support, operation, performance evaluation, and improvement. Start by obtaining the official standard document. Review each clause thoroughly. Map requirements to your specific manufacturing processes. A pharmaceutical manufacturer might focus on chemical waste management while a food processor prioritizes water usage.
Step #2: Perform an initial environmental review
Conduct a comprehensive assessment of current environmental impacts across all operations. Identify gaps between existing practices and ISO 14001 requirements. Document all environmental aspects including emissions, waste streams, resource consumption, and potential emergency situations. For example, a metal fabrication plant might discover undocumented chemical storage practices during this review.
Step #3: Plan your implementation project
Develop a detailed project plan with clear milestones and deadlines. Assign specific responsibilities to team members with environmental expertise. Allocate budget for potential infrastructure changes, training programs, and documentation systems. Manufacturing companies typically need 6-12 months for full implementation depending on size and complexity.
Step #4: Educate your organization
Provide role-specific training for all employees from executives to production staff. Create awareness programs explaining environmental impacts relevant to each department. Develop specialized training for staff directly responsible for significant environmental aspects. A packaging company might train production teams on proper waste segregation while teaching maintenance staff about managing oil spills.
Step #5: Document your environmental management system
Create a comprehensive environmental manual outlining policies, objectives, and organizational context. Develop standard operating procedures for managing significant environmental aspects. Establish documentation for monitoring, measurement, and evaluation processes. Documentation should be accessible, understandable, and regularly updated to reflect operational changes.
Step #6: Implement and operate your EMS
Roll out environmental procedures across all departments simultaneously. Begin collecting data on key environmental indicators from day one. Address non-conformities immediately as they appear. Maintain detailed records of all environmental activities for future reference and trend analysis.
Step #7: Conduct internal audits
Schedule regular internal audits covering all EMS elements and departments. Train internal auditors to look beyond paperwork to actual operational practices. Document findings systematically and track closure of corrective actions. Manufacturing facilities typically conduct quarterly departmental audits and annual full-system reviews.
Step #8: Undergo registration audit
Prepare thoroughly by conducting a pre-assessment with an experienced consultant. Address any identified weaknesses before the official audit. Ensure key personnel are available to answer the auditor's questions. Provide organized, accessible evidence of implementation for each ISO 14001 requirement. Most manufacturing organizations require 2-3 days of on-site auditing depending on facility size.
Common ISO 14001 Implementation Mistakes
Manufacturing operations often struggle with specific aspects of ISO 14001 compliance. The most frequent issues include
Lack of management commitment
Without top leadership support, the EMS often fails to gain necessary resources and attention.
Inadequate employee training
When staff members are unaware of procedures and policies, non-compliance and inefficiencies result.
Poor documentation practices
Ineffective creation, management, and maintenance of required documentation undermines the system.
BPRHub's Environmental Management Module helps manufacturers avoid these pitfalls through automated documentation, scheduled reviews, and comprehensive tracking tools.
The ISO 14001 Transformation
Before ISO 14001 Implementation:
- Environmental data scattered across departments
- Reactive approach to compliance issues
- Inconsistent waste management practices
- Limited visibility into resource consumption
- Missed opportunities for cost savings
With BPRHub's ISO 14001 Framework:
- Centralized environmental data and documentation
- Proactive identification of compliance requirements
- Standardized waste reduction procedures
- Real-time monitoring of resource usage
- Systematic approach to efficiency improvements
Integrating ISO 14001 with Other Standards
Many manufacturers already use ISO 9001 for quality management. Integrating ISO 14001 with existing systems offers significant advantages
- Reduced documentation through aligned procedures
- Streamlined audits covering multiple standards simultaneously
- Consistent approach to risk management across operations
- Lower implementation costs through shared resources
Key Takeaways
→ ISO 14001 remains voluntary but increasingly essential for competitive manufacturing
→ Implementation delivers cost savings through resource efficiency and waste reduction
→ The standard helps manufacturers stay ahead of complex environmental regulations
→ Common non-conformities can be avoided with systematic management approaches
→ Integration with other standards maximizes return on compliance investments
→ BPRHub simplifies ISO 14001 compliance through centralized management and automation
Discover how BPRHub simplifies ISO 14001 compliance by automating documentation, tracking, and reporting
📍 Book a Demo
📧 hello@bprhub.com
FAQ
Is ISO 14001 legally required for manufacturers?
ISO 14001 is voluntary in most countries. Some government contracts or industry regulations may require ISO 14001 compliance. Customers may also expect suppliers to follow this standard. In the European Union, regional directives often align with ISO 14001, so adoption can help meet legal and market requirements. For example, a supplier bidding for a public infrastructure project may need ISO 14001 to qualify.
What documentation is needed for ISO 14001 compliance?
Organizations need to keep records showing the scope of the Environmental Management System, environmental policy, list of interested parties, and documented information on environmental aspects and impacts. Operational controls, emergency procedures, and records of monitoring activities are also required. Documentation must be accessible, up to date, and suitable for audits. For example, A food manufacturer may keep daily logs of water usage and waste disposal as part of its records.
How long does ISO 14001 implementation typically take?
Most manufacturers need six to twelve months for full implementation. The timeline depends on company size, complexity, and current environmental practices. Smaller organizations with simple processes may move faster, while large plants with multiple sites need more time. Assigning clear roles and using project management tools helps keep the process on track.
What are the main benefits of ISO 14001 for manufacturers?
ISO 14001 helps manufacturers cut costs by reducing waste and energy use. The standard improves market access by meeting customer and regulatory demands. Companies gain better control over compliance risks and can respond quickly to new regulations. For example, a packaging company using ISO 14001 may win contracts with global brands that require strong environmental management.
Can ISO 14001 integrate with other management systems?
ISO 14001 works well with standards like ISO 9001 for quality management. Integration reduces duplicate documentation and streamlines audits. Companies can manage risks for quality and environment together, saving time and resources. A manufacturer using BPRHub’s Unified Compliance Framework manages both standards in one place, improving efficiency and audit readiness.